The last short-wheelbase 6-cylinder E-Type rolled off the assembly line in Coventry sometime in October of 1970 – which about a year before I was born… And based on what I have seen from other manufacturers, that means that a CORRECT E-Type outer sill has not been produced in my lifetime.
Until 9 days ago…
Click here to purchase our new PERFECT Outer Sills in our Online Store!
That was when Brent and I FINALLY managed to produce our first PERFECT outer sill. It is IDENTICAL to the factory sills in EVERY WAY – and it is NOTHING like anything else currently available – anywhere.
I have dreamed of making this part since the very day I dreamed of starting this business – though I had no idea how much time, energy, shop space, and money it would take to get it done… Everyone at the shop put their heart and soul into this piece, and the end result is nothing short of spectacular – I’m VERY proud of how we overcame the MANY obstacles along the way, and stopped at nothing until we had fabricated a 100% PERFECT E-Type outer sill!
Read on to see what makes our new sills the ONLY CHOICE for YOUR E-Type!
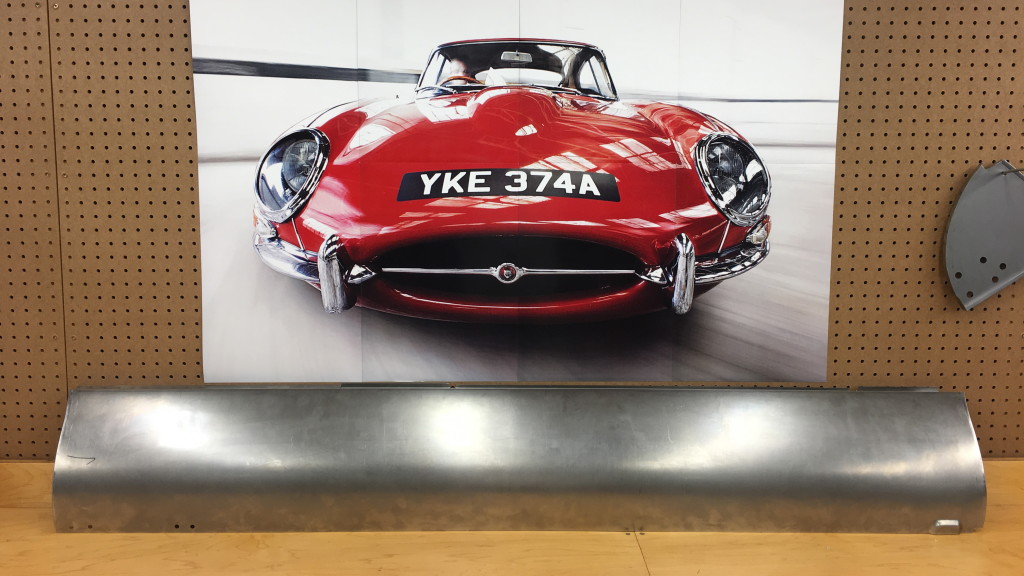
This is a new Monocoque Metalworks LH Outer Sill for all 6-cylinder E-Type Coupes (FHC) and Roadsters (OTS). It is absolutely 100% correct in every way – it is EXACTLY the same as the factory produced them – in EVERY dimension! Note how the “light line” of this sill clearly shows the drastic change in radius as you go down into the lower half of the sill – that is CORRECT!
Monocoque Metalworks has produced a new E-Type outer sill that is unmatched – ANYWHERE – in quality, precision, and most of all – CORRECTNESS! The currently available sills have no less than TEN MAJOR PROBLEMS:
Point #1) Shape – the curve of the sill from top to bottom is correct. On all other sills the curve is incorrect – it is too shallow, and one steady radius throughout the piece. As a result, near the middle of the sill – it is sunken in NEARLY 3/4-INCH – and changes the look of the car drastically when viewed from the side. Ours is correct – and as such, increases in radius as it goes under the car.
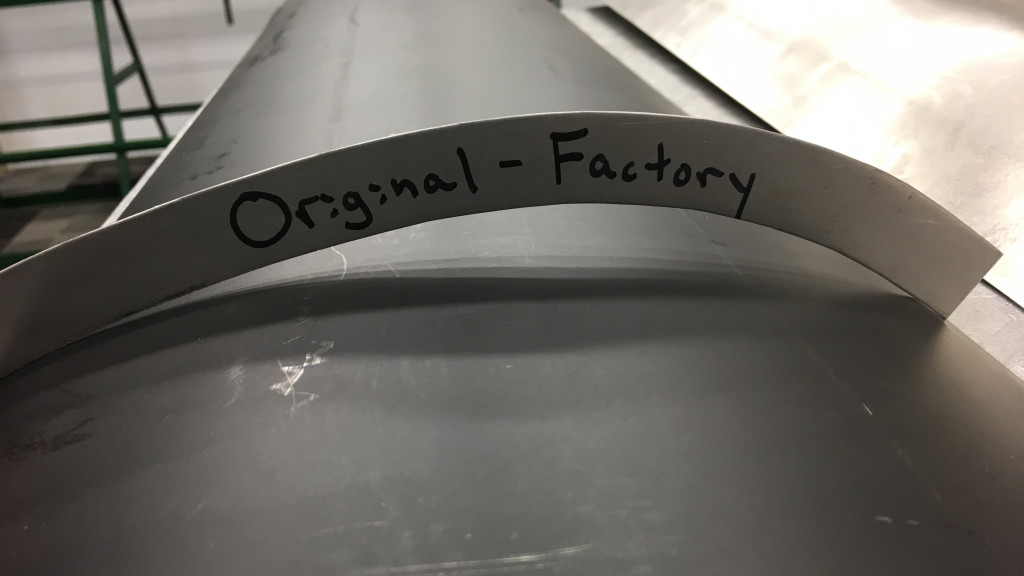
Theirs – not even close… This is a contour gauge we formed to match several “virgin” E-Types that still carry their original sills. against the commonly available outer sills from “the other guys”. If you are purchasing outer sills from ANYWHERE else, you are getting this brand in black primer, and this is how they are ALL shaped – which is VERY wrong…
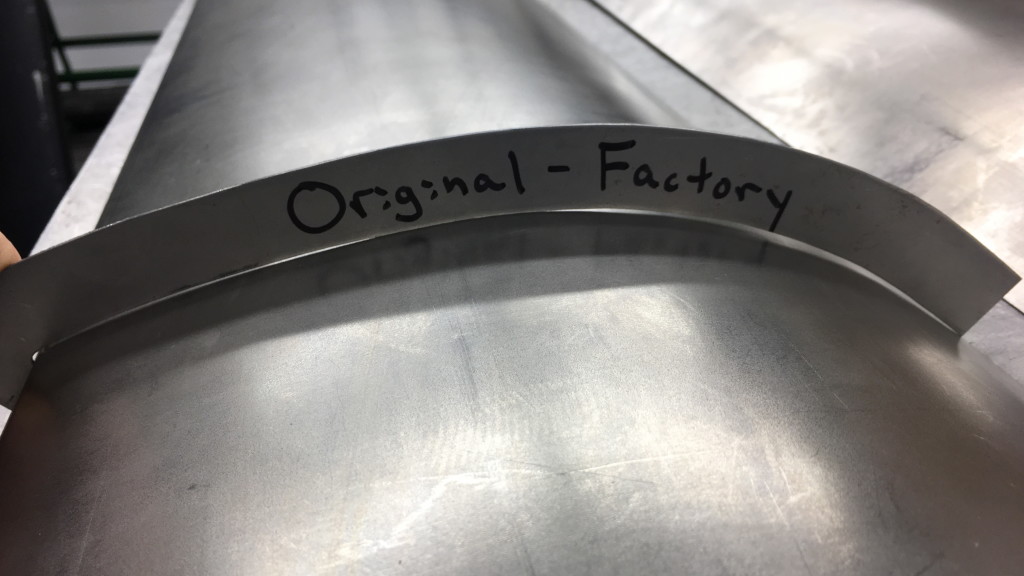
Ours – spot on… We go to GREAT lengths to make sure that every sill that leaves this factory is of the absolute highest quality, and matches this gauge precisely. This is one of the prototype sills – the production sills are even tighter to the gauge – they are EXACT – not 3/4-inch off like the only other sills that have been available up until now!
Point #2) No bottom bend. Because the other sills have the wrong radius, they MUST put a significant bend in the bottom 1-inch of the sill to get back to flat where it meets the floor. This is incorrect and our sills do not have it.
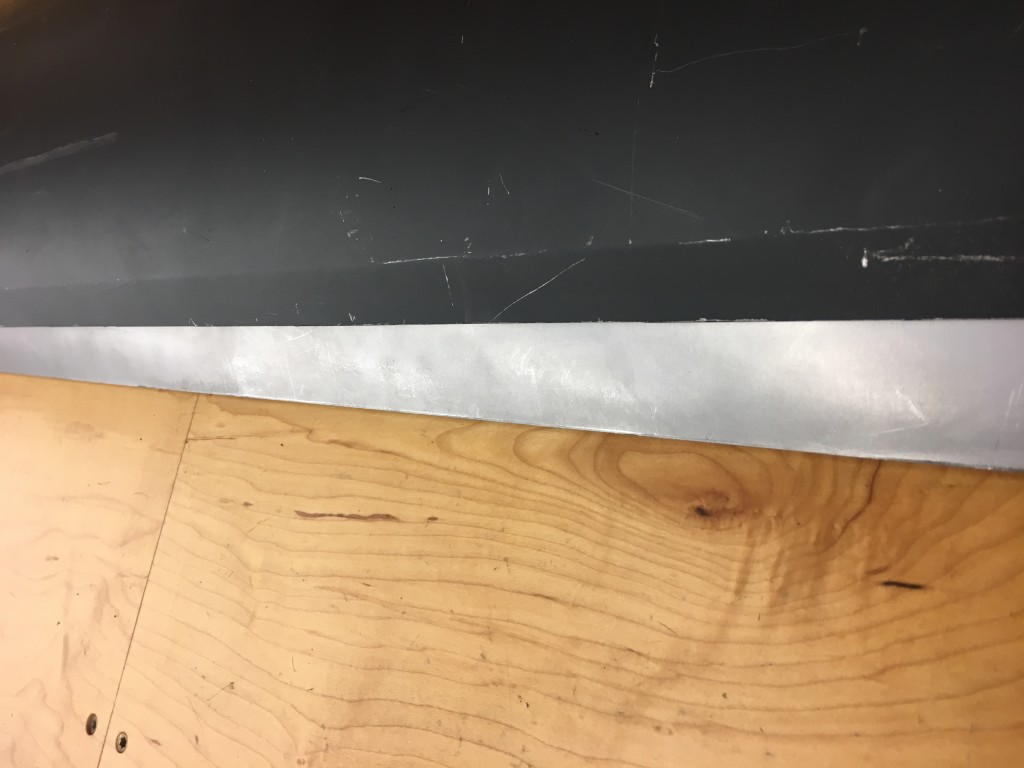
Look closely at the competitor’s sill in black – it is the same sill shown in the photo above with the contour gauge. SInce their curve is off so drastically, they chose to put this bend into thebottom edge of the sill in order to get back to “flat” against the floor. You can see this in the contour gauge photo above as well… Ours is a smooth curve all the way to the floor – as it should be.
Point #3) NO KINKS! – Getting the proper radius into the sill without a “tooling kink” was one of the biggest challenges we had to overcome – but we did! Other sill manufacturers have not, and every one of their sills has a soft kink running the entire length of the sill approx. 1-inch below the door. This has been a sore spot for many top builders, and the only way to get rid of it is to CAKE the whole sill with filler and block sand the whole thing with long blocks. Ours is a smooth transition of the increasing radius from top to bottom.
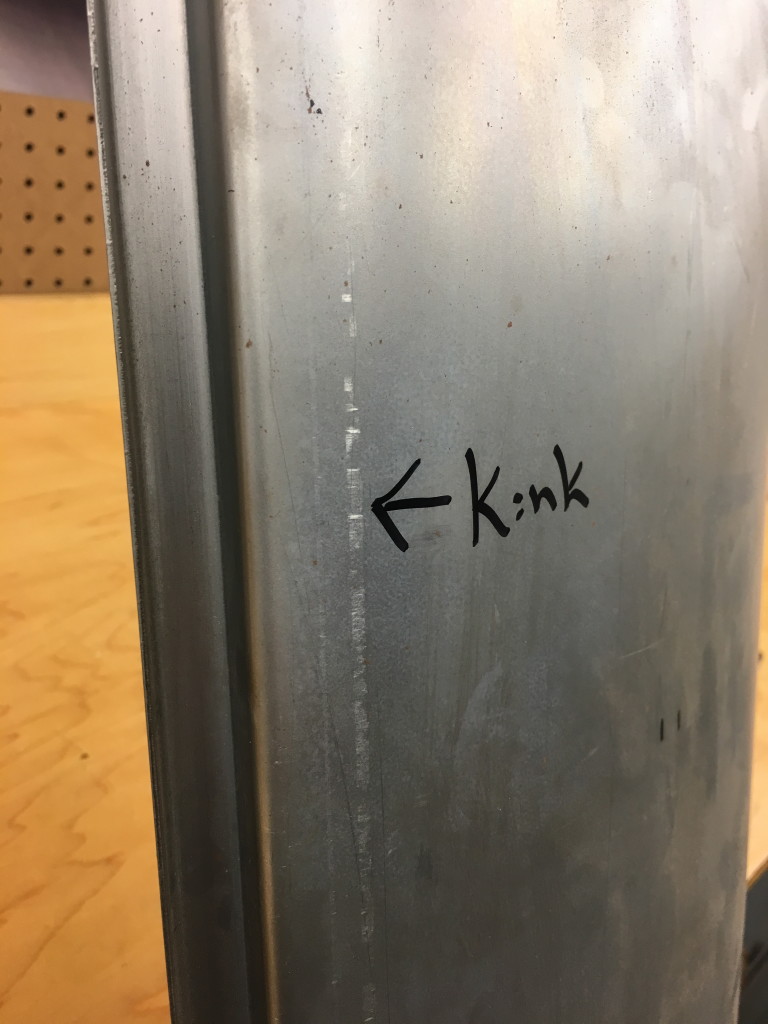
This is one of the competitors sills, stripped of it’s black shipping primer. Every one of their sills has a kink in it from the tooling they have chosen to produce the sills. It is approx. 1 inch below the door opening and runs the entire length of the sill. In this case, the tooling that made the kink has also marked the panel in the same process.
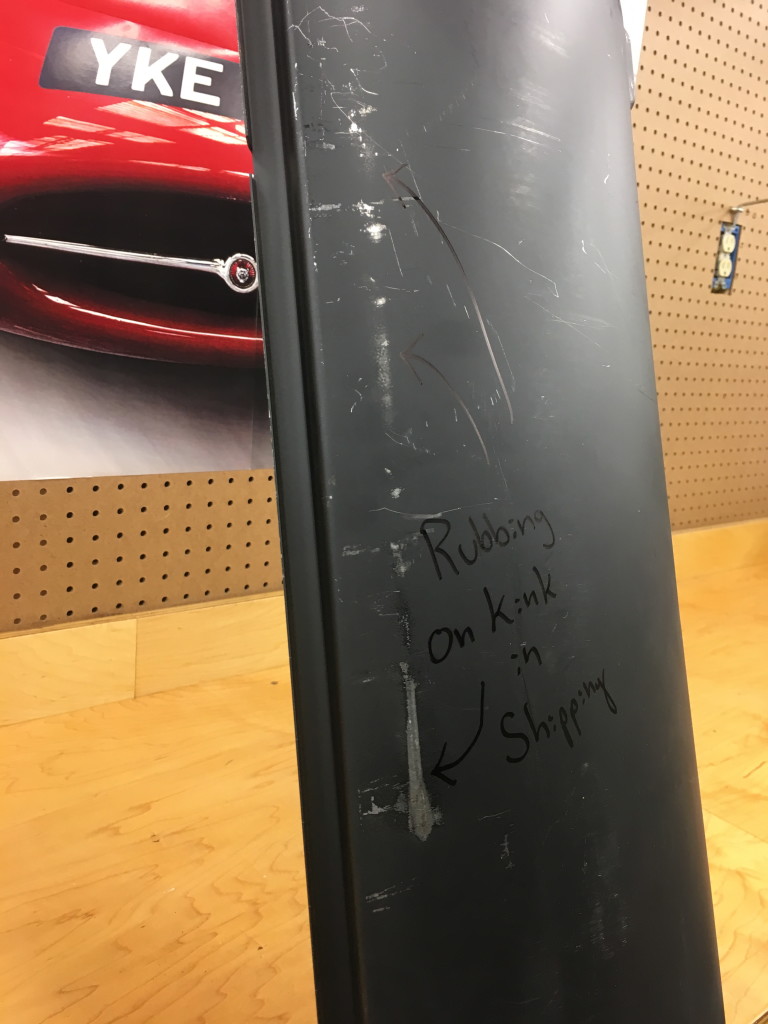
Here is another photo of another of the competitor’s sills – with it’s primer still on. In this case, this sill was shipped nested with another sill, and the black primer has been rubbed off all along the kink – which clearly shows this as a definite “high spot” that runs the length of the sill. If this kink is this noticeable now – imagine what it is going to look like in a glossy finish paint! And the only way to eliminate it if you use this sill on your E-type is to start caking on LOTS of filler…
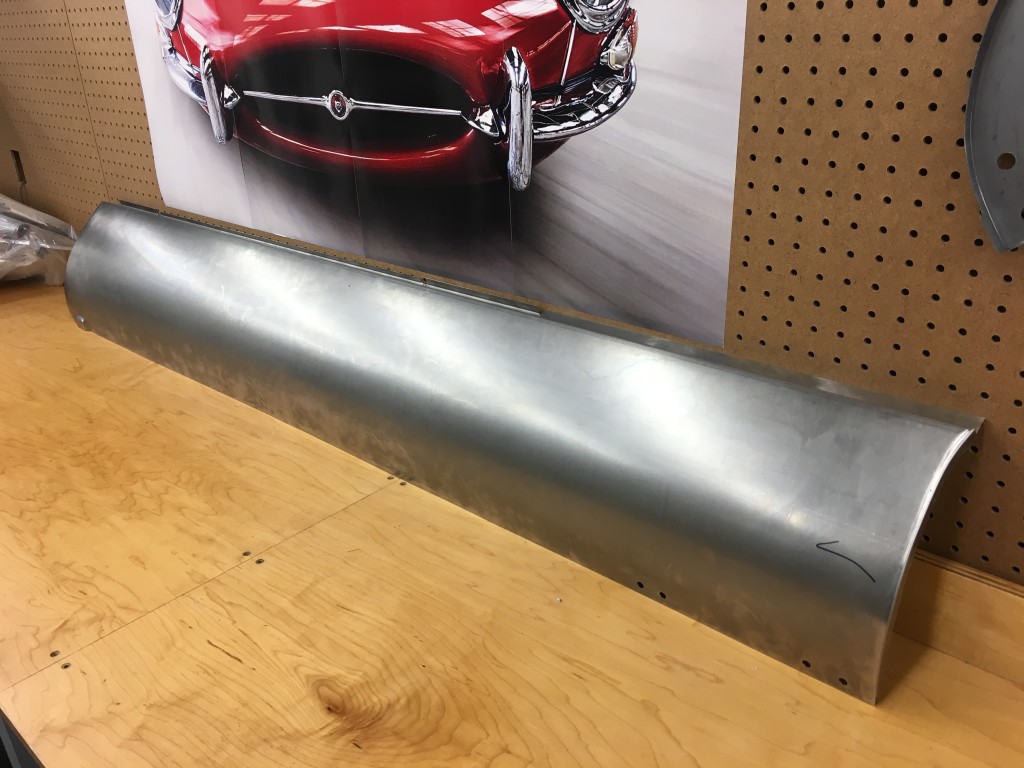
The new Monocoque Metalworks sills are not only the correct radius from top to bottom, but there are NO KINKS – ANYWHERE! Look toward the left side of the photo – the angle of this shot gives a good view of the increasingly tight radius as we reach the bottom of the sill.
Point #4) Correct width sealing channel below the door. We have carefully determined the correct width of the sealing channel that runs the length of the sill below the door, and have made it as narrow as it should be. This channel is too wide on the other sills out there, and you end up with a VERY wide gap below the door.
I do not currently have a good photo showing this difference, but I will add one soon!
Point #5) Crisp – and complete – corners. The upper forward and rear corners of our sills are sharp and come into full contact. The other sills have a HUGE gap up in the corners, that is a MAJOR issue for body shops.
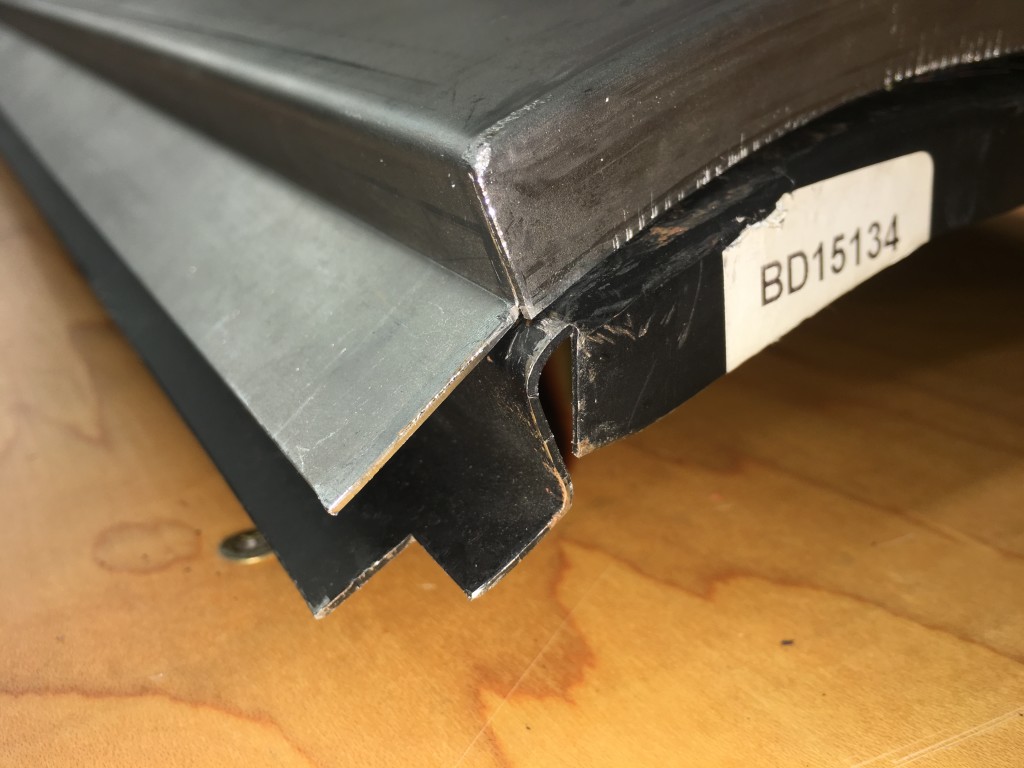
A comparison of the forward, upper corner. The Monocoque Metalworks sill is on top, the other brand available is on bottom – the VERY bottom – well below what is even remotely acceptable I would say… And they ALL look like this – this is not an exception. If your body shop attempts to solve this problem with plastic filler – or even lead – you are going to have BIG problems down the road!
Point #6) Crisp, tight bends. All of the machines and tooling we purchased for our outer sills are engineered for one purpose – to make a perfect sill. So we have dialed in a VERY crisp bend at the top edge below the door – identical to the factory sills. The other sills have a very SOFT bend here, making the gap below the door seem even wider, and if filler is used to make it crisper, it will eventually flake off…
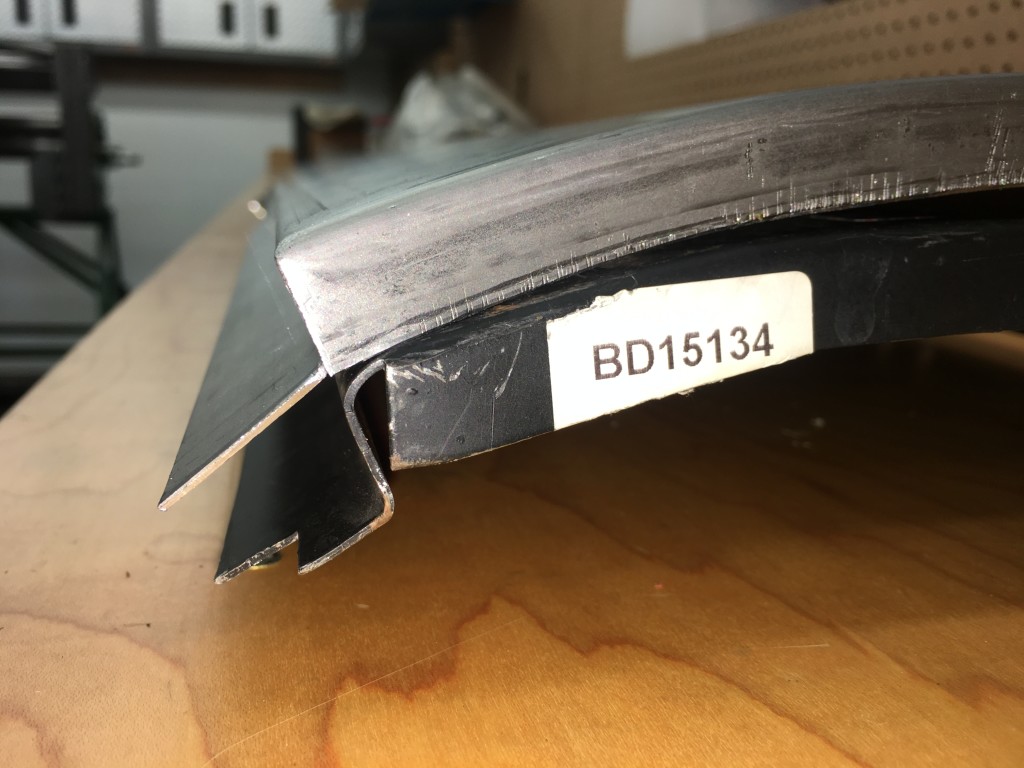
From another angle, you can clearly see that the Monocoque Metalworks sill on top has a MUCH tighter bend radius on the top edge than the competitor’s sill. This gives a very poor look to the door and bonnet gaps, and if compensated for with filler to crisp it up is also just asking for trouble when it start to flake or chip off in the years to come!
Point #7) Smooth leading and trailing edges. Our forward and rear edges are folded over and shaped by hand – it takes time (and it makes your arms tired!), but it ensures that they are smooth and uniform. The other sills are machine stamped and are “lumpy” beyond all reason… What’s worse, if you smooth out the lumps with a hammer and dolly, it changes the shape of the sill – it’s not correct anyway, but doing this will make it even worse…
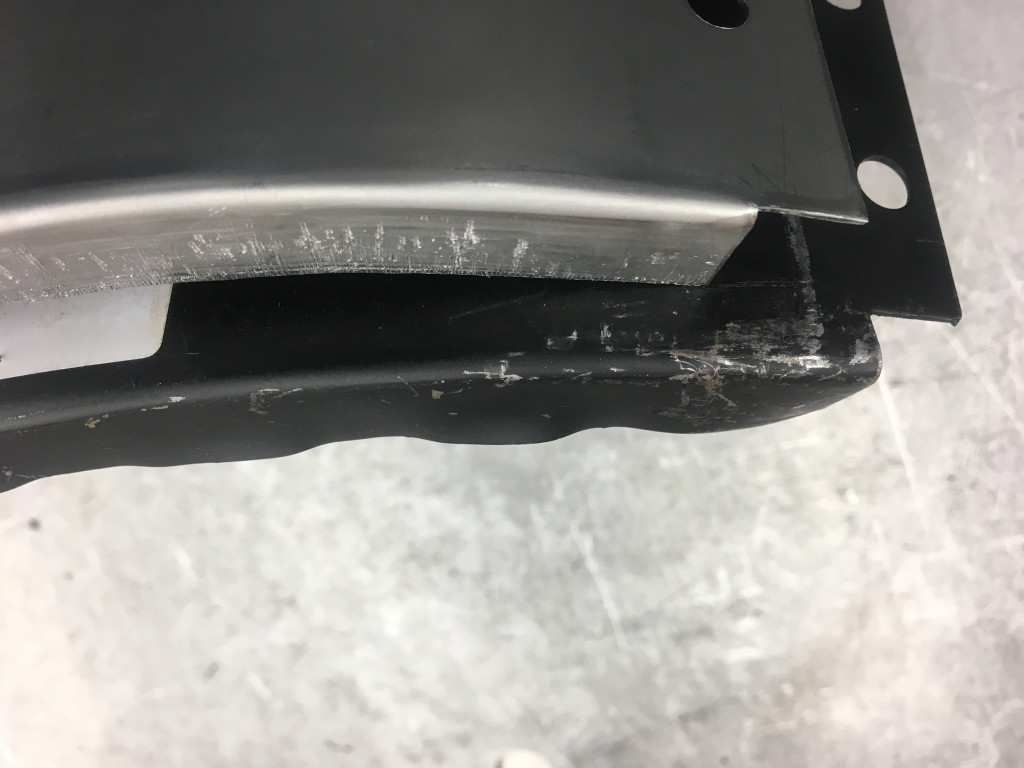
The forward edge of the Monocoque Metalworks sill – on top – is hand shaped to precisely match the factory contour, while also being dead flat and smooth. The competitor stamps their edges down in a machine, creating a VERY wrinkly, lumpy edge that needs lots of metalwork that your body shop may not even be able to accomplish effectively. Also note that the front lower corner of their sill is notched in where it should not be…
Point #8) Correctly shaped rear drain hole. Our rear drain hole is an EXACT replica of the original. Theirs is less than half of the width that it should be, and as a result, when their sills are welded on, the drain hole is completely covered.
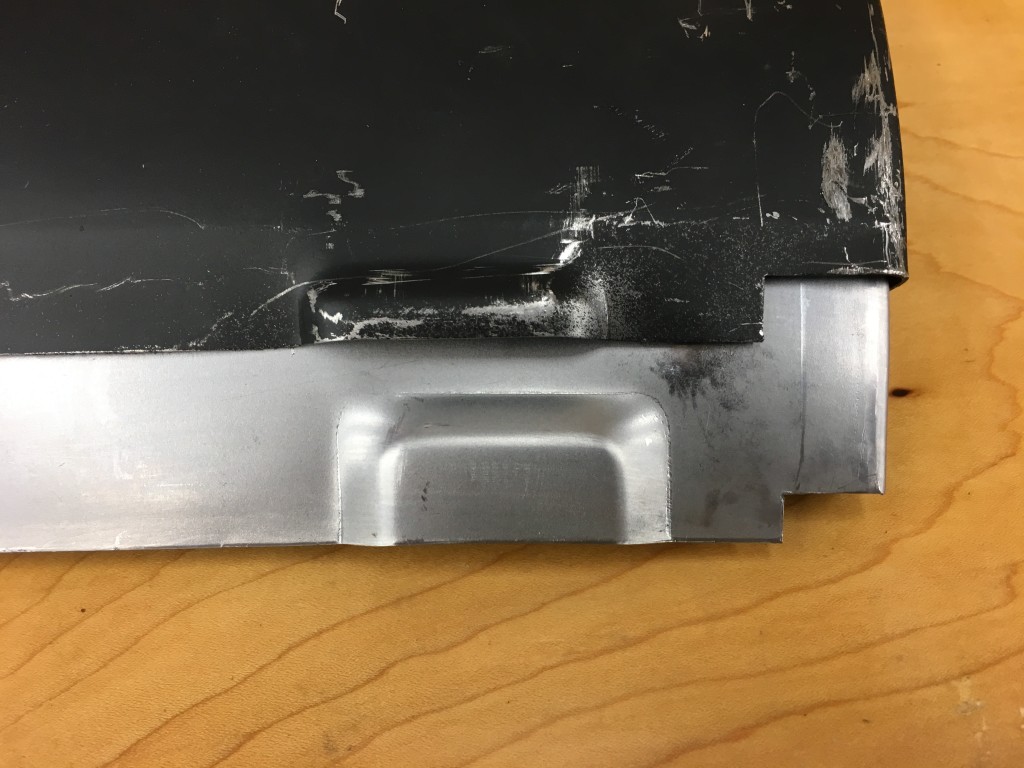
The Monocoque Metalworks sill – on the bottom of the photo in bare cold-rolled steel – has a rear drain hole that is EXACTLY like the factory sill. The competitor’s rear drain hole is too shallow (and slightly too far forward…), and is usually completely sealed off once the sill is installed…
Point #9) No front drain hole on Series 1 and 1.5 sills. The currently available sills have a double-teardrop shaped drain hole in the forward section of the sill. You would not believe the number of people I spoke to who had no clue what the origin of this strangely shaped drain was… Finally, a helpful user on Jag-Lovers send us photos of a virgin Series E-Type that has this – confirming that it is a Series 2 thing. We HAD already confirmed that all Series 1 cars DID NOT have it for sure – and also know that at least SOME Series 1.5 cars did not have it either. We will continue to try and determine an exact break point where this forward drain was added.
So this looks like an “improvement” to the cars that was added later on – although who knows if it ultimately let moisture out or water in… We will be offering the sills in BOTH configurations:
Series 1 and 1.5 E-Types – we will produce original style sills WITHOUT the front double-teardrop drain holes.
Series 2 E-Types – we will produce original style sills WITH the front double-teardrop drain hole.
Your choice – Replacement sills have been produced WITH this drain hole since E-Type production ended – undoubtedly simply because that is what was being produced at the end of the production run. If you have a Series 1 or 1.5 and DO want the double-teardrop drain, we will certainly press them in for you at no additional charge – you can have the sills either way!
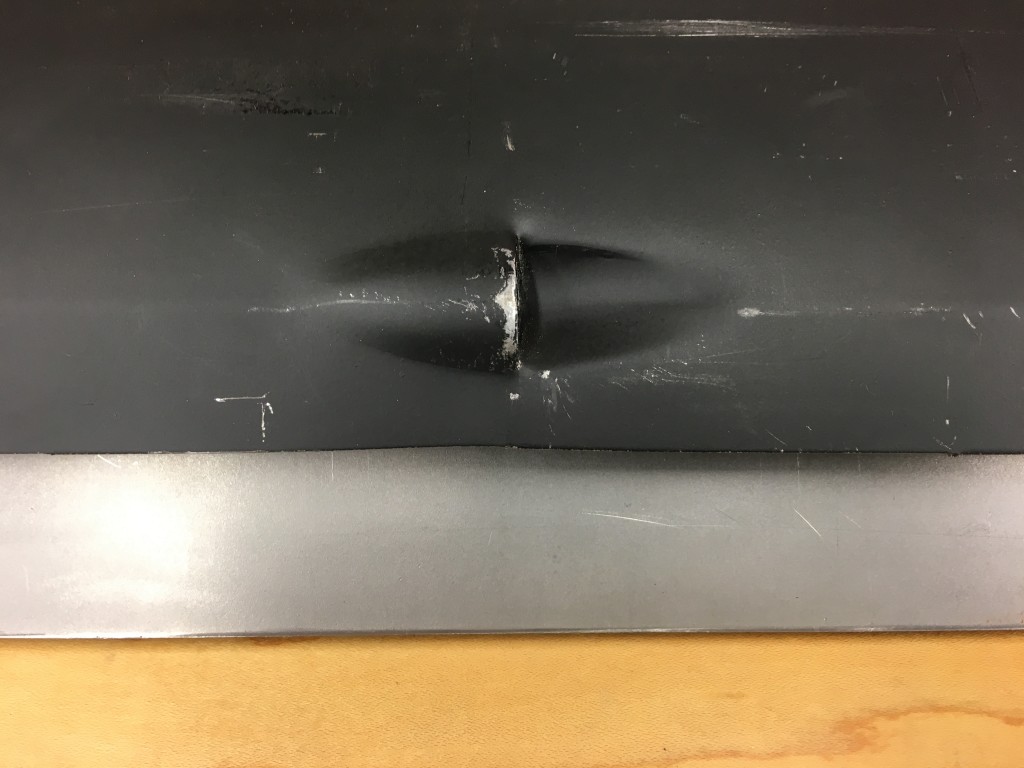
The other outer sill manufacturer punches this double-teardrop drain hole in the forward end of all of their sills, even though only Series 2 cars came from the factory with this drain. We manufacture the sills with or without the drain hole – the choice is yours!
Point #10) Correct length. We have carefully checked the sill length on multiple “virgin” E-Types and are spot on for length. From what I can tell, the other guy’s sills seem to be about 1/8″ too short – although it’s tough to tell based on the variances in the products they send out the door…
I do not currently have a good photo showing this difference, but I will add one soon!
Point #11) Delivered in Fresh, BARE steel. This is not necessarily a dimensional issue, but it is still worth mentioning. Our sills – like all of our panels – are shipped in fresh, bare cold-rolled steel with a light coating of a very thin oil – simply wipe with Acetone and start welding. The other sills will need to have their low-quality black “shipping primer” removed (or you’ll be sorry!) – and it is a messy, time consuming task. Although, I will admit that it will allow you to clean off some of the surface rust they have painted over in many cases…
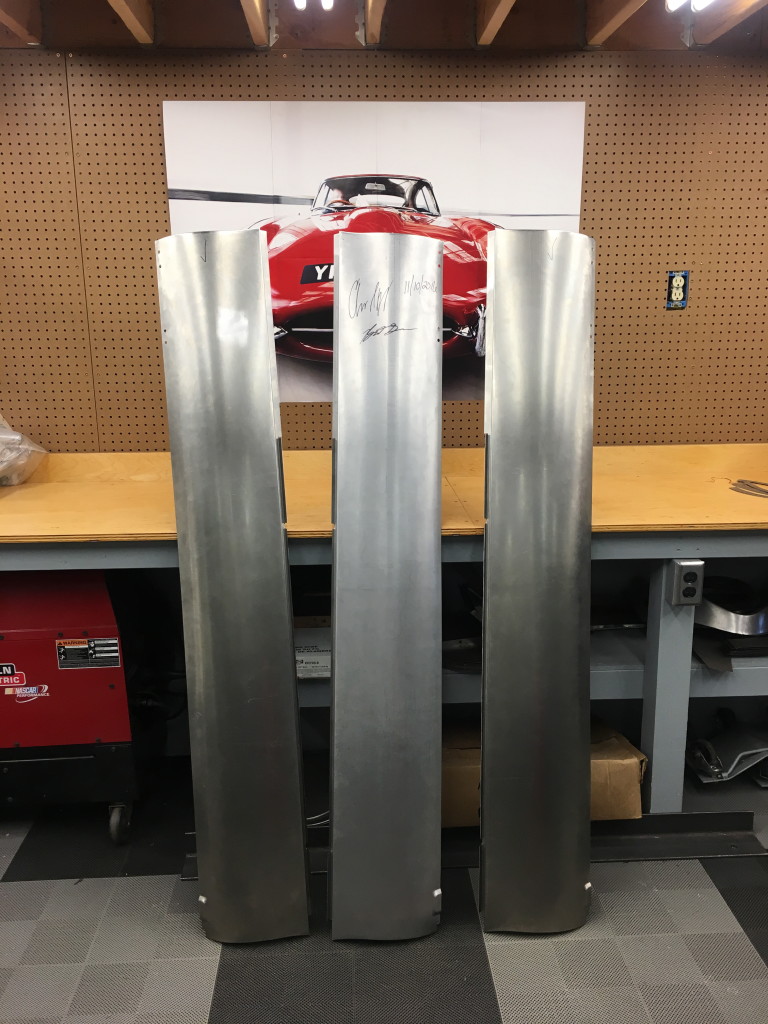
Our sills are always delivered in fresh, bare, cold-rolled steel – you won’t have to spend time and energy on the messy job of stripping the black shipping primer. This shot shows the 4th prototype sill – which turned out to be the first one that we were able to fully complete. I ran around the shop like a crazy person, screaming with delight after this 18-month adventure, and then Brent and I signed the sill and hung it on the wall. But not before taking this photo, where it is flanked by the first pair of Monocoque Metalworks production sills.
Conclusion:
So, what this all means is that if your E-Type needs new sills, and they are not yet installed, you simply MUST make sure that a pair of our new sills is your only choice! I’m not saying this as a sales pitch, but rather, as an E-Type enthusiast who wants to help you restore your shell as well – and as correctly – as it can be done. AND to save you a world of headaches in the bodywork phase!
Give us a ring today and reserve a pair for YOUR E-Type! Trust me – it will be one of the best investments you can make in the restoration of your monocoque body shell!
Background:
If you take a good look at what it took to get this done, you’ll understand why it has taken us this long to make the most commonly asked-for part on the entire car. We have been able to make the curves and bends needed in shorter lengths for years – but as the length of sheetmetal increases, the force required to form it – properly – goes up exponentially. And so we had to buy some BIG machines to get the job done right. And unfortunately (or fortunately in hindsight) purchasing those machines was the “straw that broke the camel’s back” and what pushed us into the new, much bigger shop last year.
Everything that is wrong with the “other guy’s” outer sills is a pure function of making it easier to mass produce. In looking at all of the problems with them over the years, we have constantly asked, “Why would you do it like that!?!” – Well, now we know… And over the past six months, we have said many times, “OK, THAT”S why they did that!” – and in EVERY SINGLE CASE it makes the production process much easier, while making the correctness of the sill much worse!
Some of the machines we purchased solely to make the sills worked great, and did just what they were supposed to do. Others failed miserably – and in several cases, we had no choice but to build our own special machines to get certain parts of the job done. Some were small tooling items – while others were MAJOR projects where we were essentially “reinventing the wheel” – building a machine from scratch that already exists – but none exists that does the job JUST RIGHT….
The end result is nothing short of ABSOLUTELY 100% PERFECT Outer Sills. I can’t stress this enough – they are flawless. Crummy (horrible, really) outer sills have been readily available forever – and so you should understand that I did not go to all of this trouble to make something else that is not right in some way.
I started this project for several reasons – mostly just to continue the lifelong quest of building the whole car from scratch – perfectly. BUT I also just got tired of selling customers a whole package of excellent panels – minus the outer sills – and telling them, “OK – here are the part numbers of the outer sills, here is where to buy them – and Oh, by the way, they don’t fit at all…”
And so for this E-Type fanatic – it’s about getting a correct sill out there on the market so I can be part of the solution to making the cars the way they should be. And BELIEVE ME – the cars look substantially different with the currently available sills than they did when they rolled off the assembly line!
So take a careful look at the photos – I think you will agree that we have done everything we can to make a proper sill – and that the current stock of the “other guy’s” outer sills is now nothing more than scrap metal… As a matter of fact – that’s where all 6 of the brand new ones I had on hand just went – and it felt GREAT!