E-Types rely on their monocoque (or unibody) structure in place of a typical car’s frame. Therefore, a solid, straight, properly repaired body shell is an important foundation for your restoration – and a MUST for your safety! Let our experience with this specialized repair ensure perfection!
Monocoque Metalworks is a unique E-Type shell restoration facility! The marriage of our shell restoration service and our E-Type Panel fabrication shop is a winning combination! By making all of our own panels, we can ensure that every single piece of your shell is IDENTICAL to the original specs. This also means that we also don’t have to wait for back-ordered panels to arrive for your restoration to continue. Once begun, your shell progresses rapidly and is back in your hands quickly!
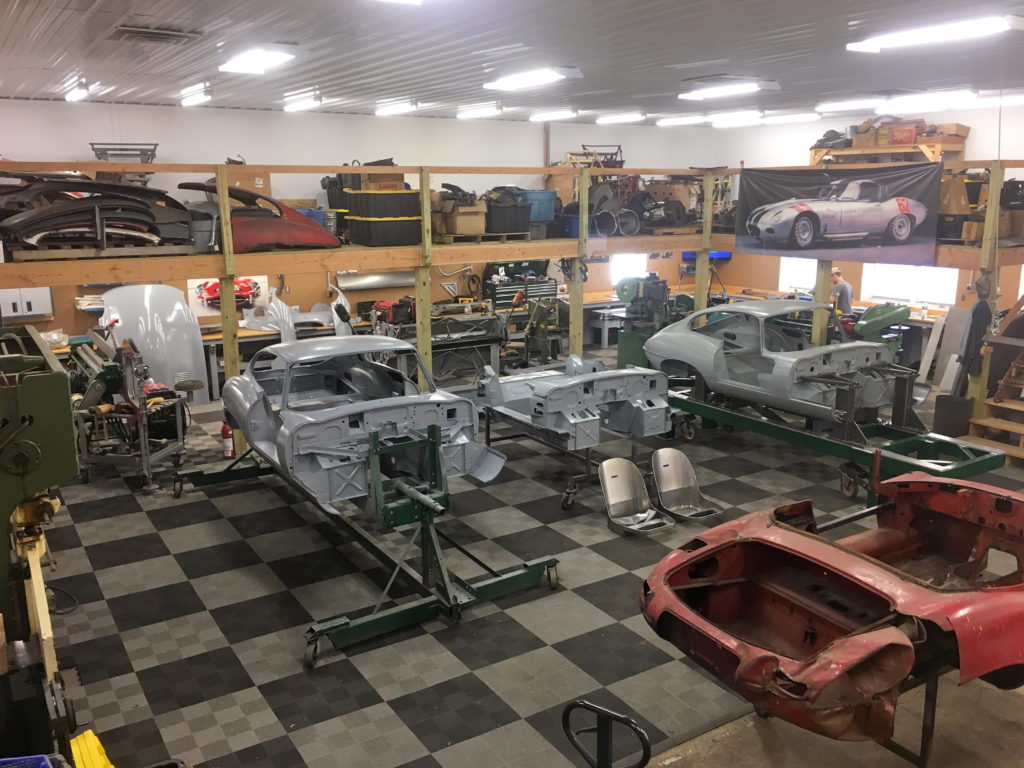
This recent shop photo shows several E-Type shells nearing completion. On the left is a 1966 FHC in our rotisserie – built over 25 years ago specifically for E-Types, it has been used over the years to restore DOZENS of body shells! On the right is a 1961 flat-floor FHC in our new chassis table – painstakingly built over 2 years by me personally, it is undoubtedly the most precise E-Type jig in the world. In the middle is a partial shell that will be skinned in aluminum as a low-drag-coupe replica. And finally, in the foreground is a very solid, but also very wrecked 1961 flat-floor OTS, waiting for restoration and re-alignment to begin. We also restored the bonnet pieces in the background, and even fabricated the 3.8 FHC seat shells!
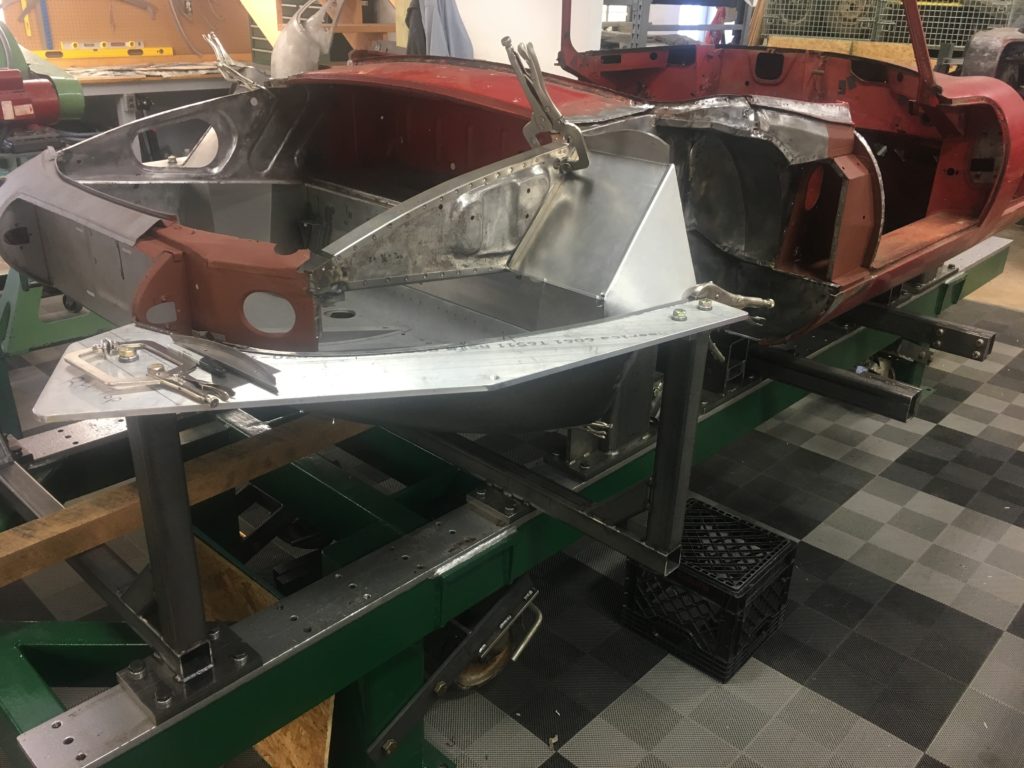
Fast-forward a few months, and the 1961 flat-floor OTS pictured above is now mounted into our E-Type chassis table and jigs. We are re-aligning the shell and restoring it, using as many of the original panels as can possibly be saved, per the owner’s wishes. Our table and jigs are EXTREMELY precise – carefully built using more than a dozen original E-Type body shells for reference. What you see here is only a small portion of the jigs we built – when they are all installed at once, you almost can’t even see the shell! They are comprehensive, and are used to make sure that every point of your shell is where it should be, to ensure a perfect fit for ALL components.
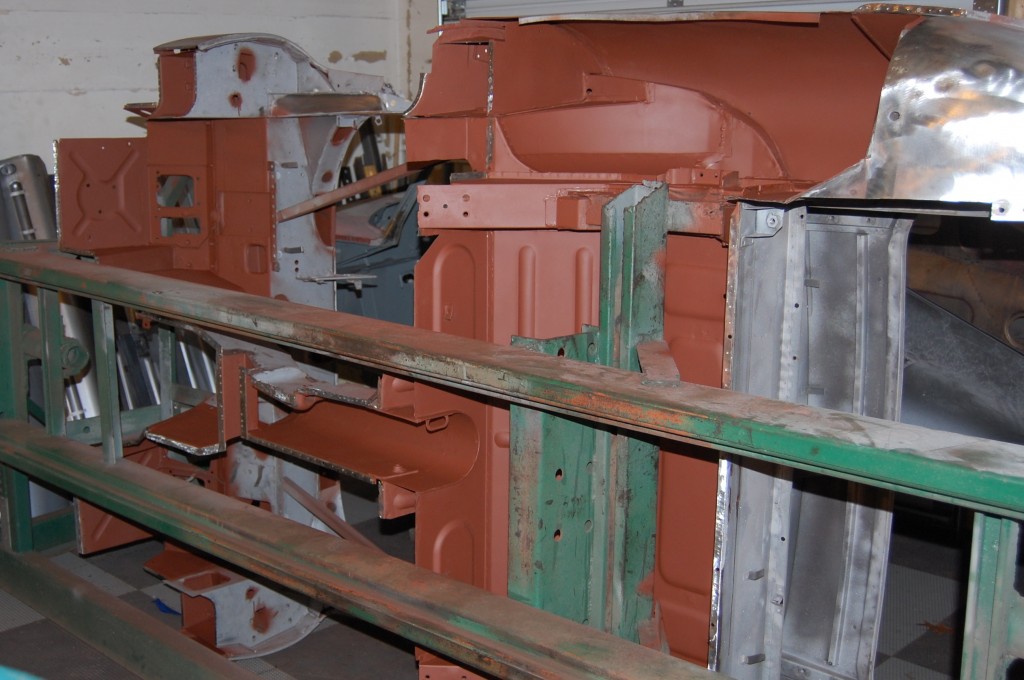
We don’t play around here – we go ALL OUT on every shell that goes through our shop! Every square inch of the shell is blasted – inside and out, and ALL cancerous rust is removed – period! ALL enclosed areas are liberally coated with quality paints and sealers, and THEN we start putting things back together!
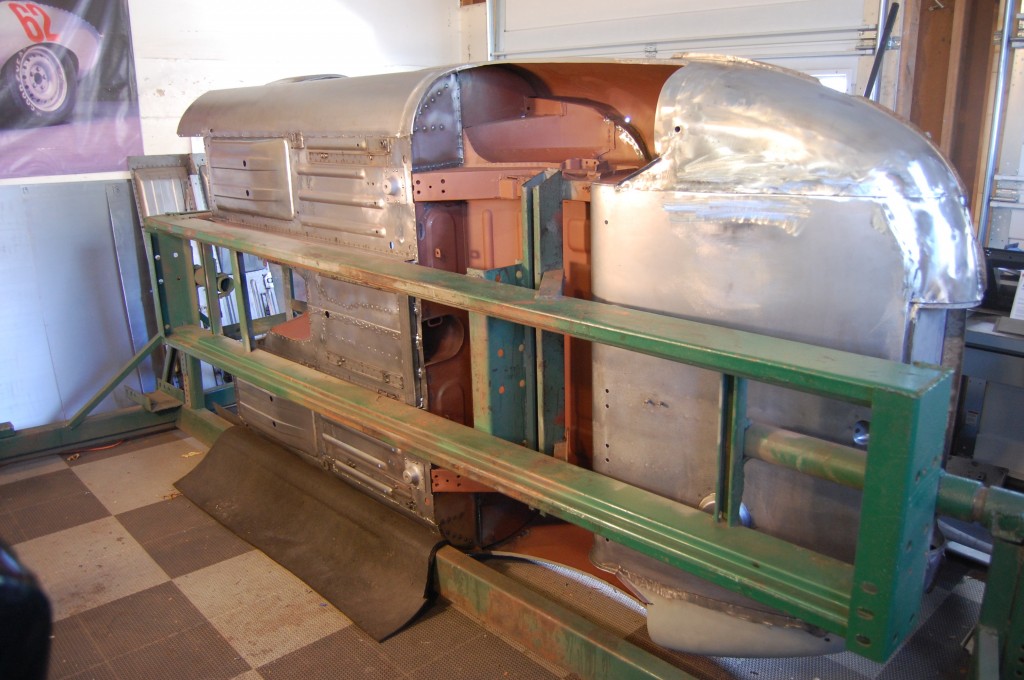
Here she is – a few weeks later! This shell now has new floors, inner and outer sills, all closing panels and gussets, new boot floor, repairs to the rear wings and lower rear valances, AND… one of our signature “hidden subframes!” You can follow the restoration of this shell from start to finish in our blog entries for this project – “1968 Open Two-Seater – GP.”
Inspection, disassembly, paint and rust removal. Your E-Type body shell will be inspected for rust and accident damage, and a ‘plan of attack’ will be agreed upon concerning which panels will be restored and which will be replaced. The monocoque will be carefully disassembled and stripped with a combination of methods we have perfected over several decades of trial and error to get the shell absolutely bare – WITHOUT damage or the sandblast warpage we often see. We do it ALL in-house, to ensure that your shell is safe!
Rotisserie restoration. The bare shell will then be mounted into our ‘rock-solid’ rotisserie to ensure perfect alignment throughout the restoration. Unlike many other shops, we use a rotisserie that does not rely on the tub itself as a part of the rotating structure, and allows quick and easy 360-degree rotation. This level of access to the shell means that we don’t have to make ANY compromises in welding techniques or quality during repair.
Shell preparation. Next, all panels to be replaced will be carefully removed with professional tools that minimize or eliminate damage to the panels that will remain. The tub will then be coated in PPG DP-series 2-part epoxy primer, and the remaining bad metal removed and the flanges of remaining panels restored.
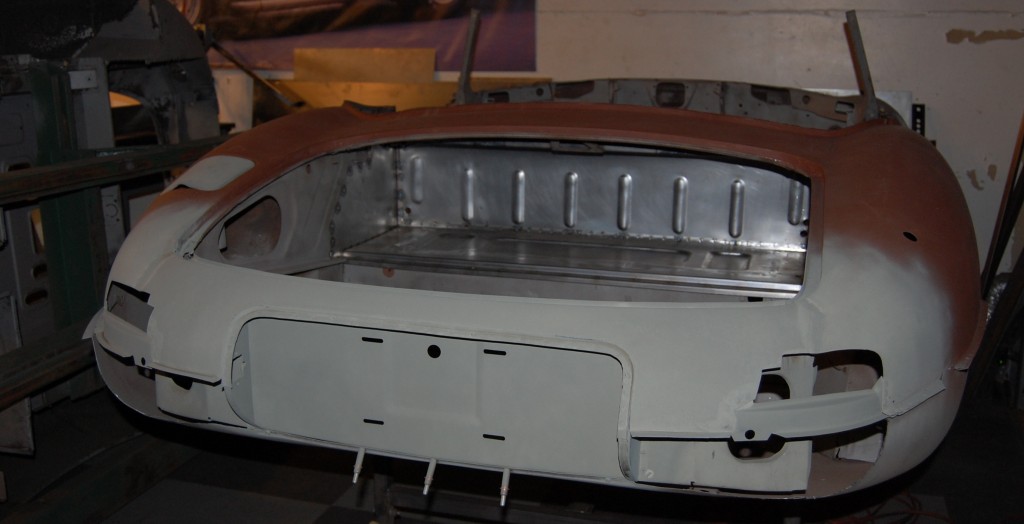
Wish your Series 2 E-Type was a Series 1? NO PROBLEM! Converting the tail of this Series 2 roadster shell was just SOME of the work we performed for this customer – here is a shot during the work. Look for hundreds more photos in the blog entries on the right – this is the “1967 Open Two-Seater – BB” project. The Series 1 roadster shell in the rotisserie on our banner photo at the top of the website also started life as a Series 2!
Panel Replacement. New panels will then be welded in using a combination of methods including Spot, Plug, MIG, and TIG welding, depending on what the specific panel or repair calls for. We duplicate the original assembly methods as closely as possible, while also adding strength and safety to the structure. All spot-welded flanges will be coated with ‘weld-through’ zinc-oxide primer before assembly. Our welding equipment is top-quality, industrial-grade machinery, and our welding skills have over 20 years of experience behind them – you can expect, and your shell will receive, absolute perfection in every single weld.
Perfect alignment is constantly ensured. Throughout assembly, the alignment and dimensions of the tub will be checked and re-checked. Our new E-Type chassis table and jigs are almost certainly the most precise in the world, and they will be used to ensure that your shell is DEAD-ON in every dimension. In addition, the fit of doors, decklids and hatches, top frames, front subframes, and the bonnet will be continually checked throughout the process.
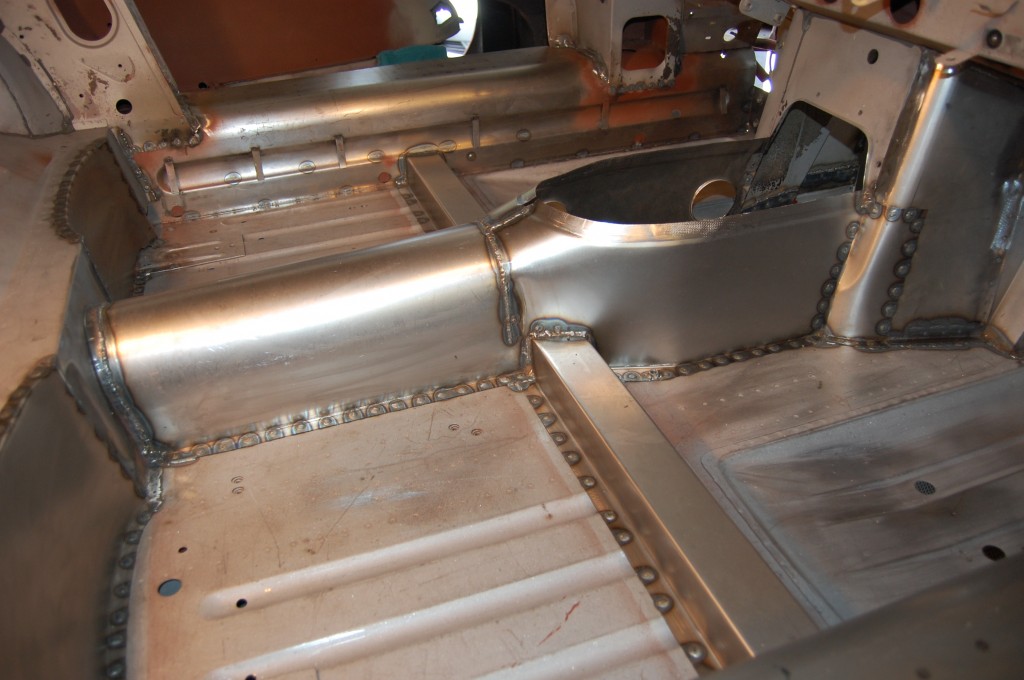
…but it will soon be replaced by pride and confidence when you see what you are going to get back! This is the same E-Type, I assure you! Don’t believe it? – follow the restoration in our blogs – this is “1963 Fixed-Head Coupe – AB”
Because our shop is specialized, we can complete this work at a VERY reasonable cost. The fabrication of our own perfect panels means MUCH lower materials cost for your project. Time and cost are also saved by eliminating the need to “fit” other manufacturers less accurate panels – our panels ALWAYS fit. All of our machines and jigs are setup for E-Type shells, and your project moves through the restoration process quickly and efficiently, saving time and expense.
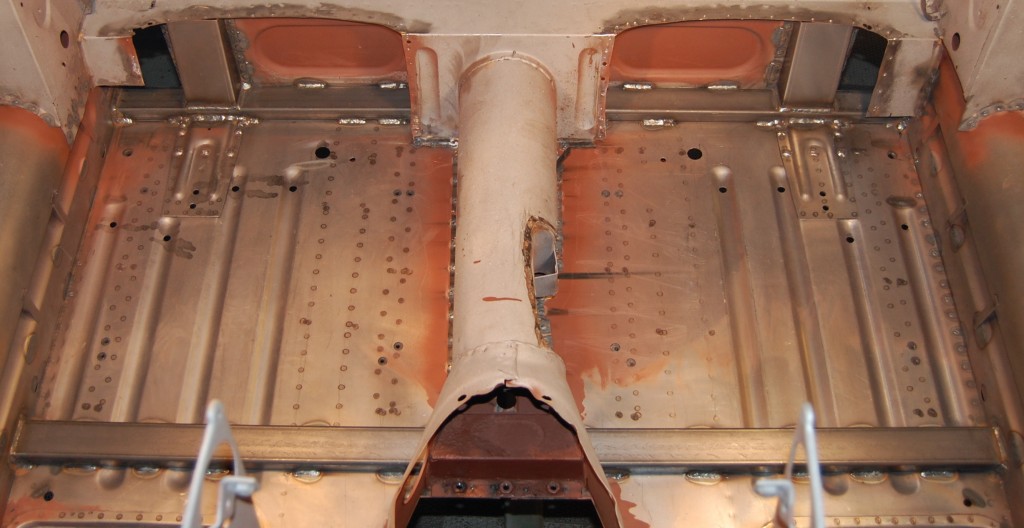
After 25 years of experience driving, racing, wrecking, and restoring E-Types, we have figured out the best way to reinforce the shell to add strength and safety to the monocoque. This shell has had our “hidden subframe” installed, but not yet hidden in this shot by new crossmember halves and rear bulkhead seat dishes. Our design introduces roll-cage strength rectangular tubing into the structure. It adds safety in the event of a side collision, and beefs up the engine frame rail mounts, rear radius arm mounting cups, and even the jacking point! Often imitated – but never duplicated… We have these cars dialed in – we know what they need and how to do it right!
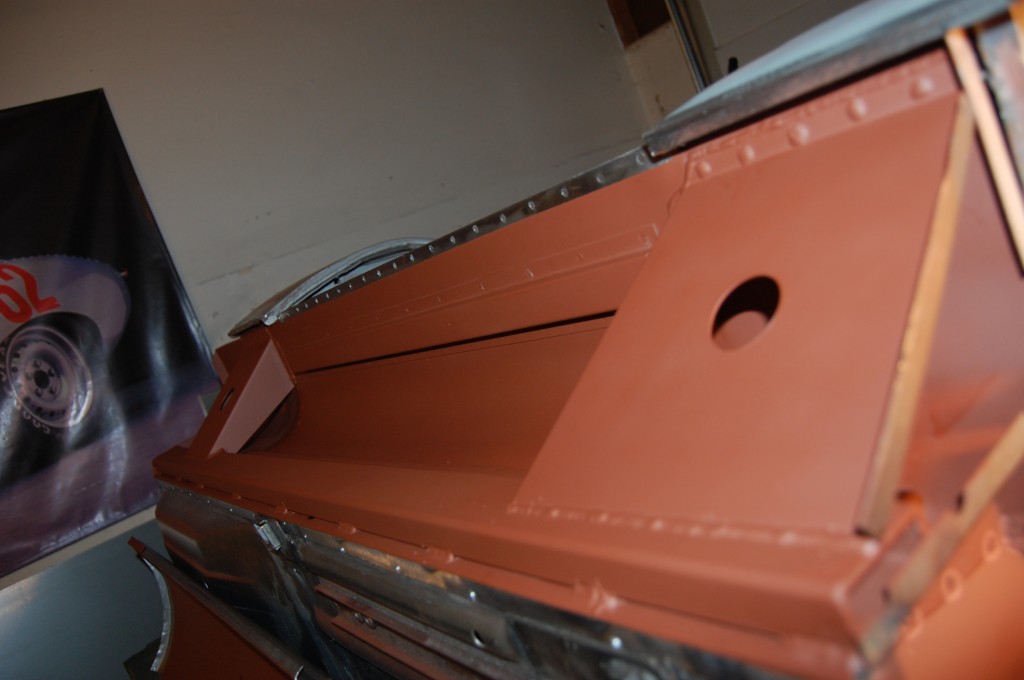
Body shell flex, chips along the edge of the rear doors, and eventually the inability to close or open the doors are all distant memories for this 1968 Roadster. There have been many different attempts to stiffen the sills of these cars – extra gussets, sheetmetal tie-ins with fancy little holes in them – you’ve probably seen them on other forums. They are all TINFOIL compared to our 12-gauge tubing and thick 16-gauge gussets. On our shells, the passenger cockpit is essentially boxed-in with a “flat roll-cage.” AND – it’s an inexpensive addition that only adds 32 pounds – a small price to pay for the added stiffness – and safety! More details and MANY more photos in “1968 Open Two-Seater – GP.”
In conclusion, we are the answer you have been looking for! We can restore ANY condition E-Type monocoque to indistinguishable from the day it left the factory. There is no such thing as a ‘parts car’ at Monocoque Metalworks – you can bring us your shell in TWO PIECES if it is that far gone – NO PROBLEM! We can also make improvements and modifications if you desire, such as extra internal gusseting, improved radius arm mounting points for high horsepower applications, roll bars, etc. We can even convert a coupe tub to a roadster if you wish! Give us a call and let’s discuss your project today!
Monocoque Metalworks – (443) 907-2287 – Chuck
chuck@monocoque-metalworks.com
References available – or come visit and see our tools and skills in action!